lead laser department and trained a team of 10+ at saitex’s first mini factory in the usa
saitex usa est. 2020
During my work experience at Saitex USA, I was taught how to operate two different laser systems, the SEI Flexi Denim 2C and SEI Matrix Textile lasers. These lasers etch the worn looks “whiskers” and fades into raw denim that is then washed. This process is originally done by hand but lasers expedite the processing and is better for worker’s health.
I trained and supervised a team of over 10 operators and a junior graphic designer on laser operation, including how to adjust the designs for sizing and editing. I provided instructions, notes, and feedback while fostering a collaborative team environment. Additionally, I was part of a dynamic team that navigated the challenges of working in a manufacturing facility during the COVID-19 global pandemic.

Reviewing Jr. Graphic Designer design edits

Worked through first outbreak of Covid-19, Factory never shut down

Compiled a library of designs for customers to peruse
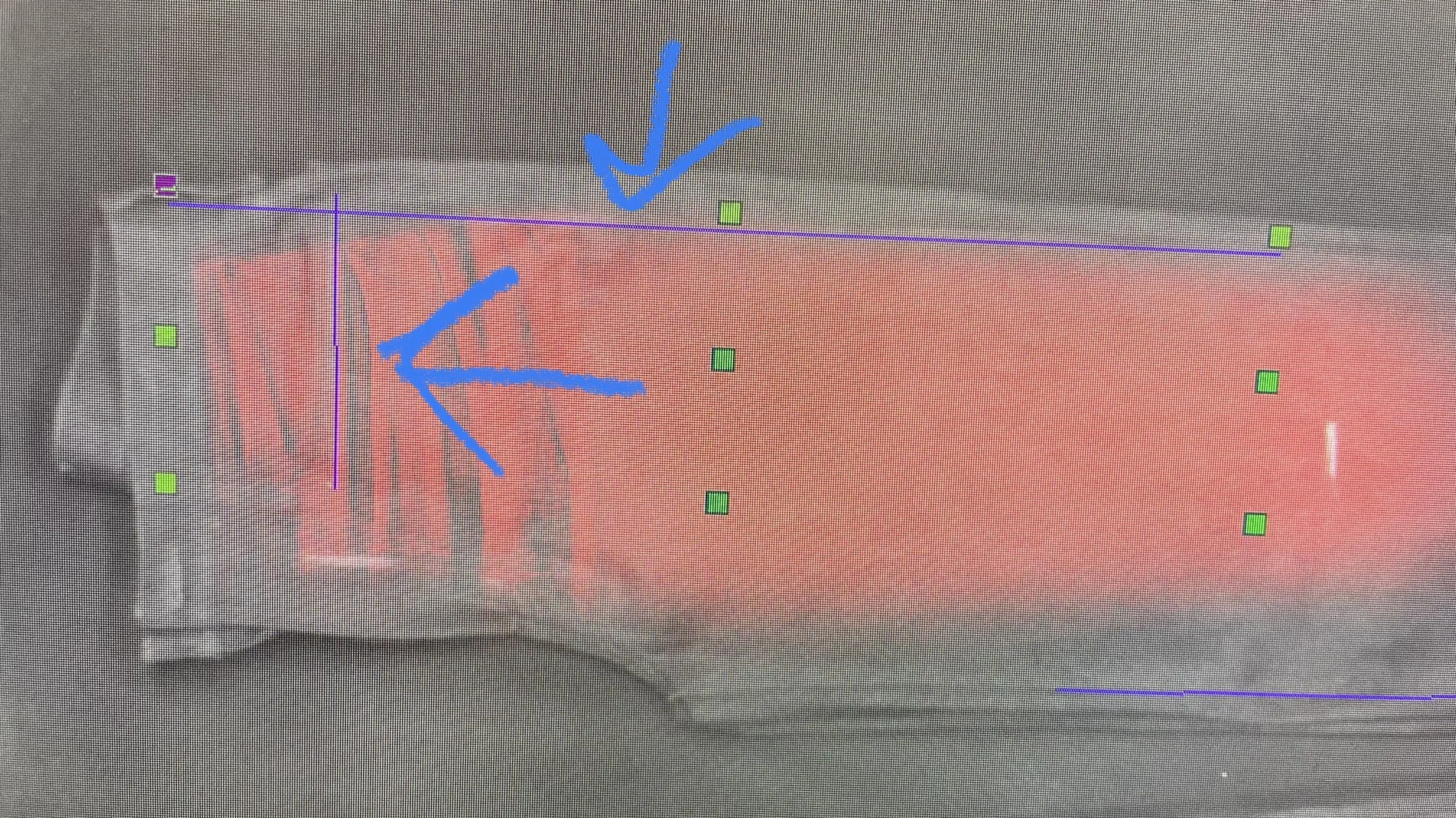
Guideline placement instruction for operators
Designed a inventory sheet for operators to keep track of how many jeans were burned per hour
Early User of First-of-its-kind laser technology :
the Sei matrix textile laser
If you are lucky enough to be offered the opportunity to learn a new technology in a work setting and how to operate a first-ever-prototype-of machinery—definitely take it. It was a challenge and included many hours of being taught in on the job and from passionate technicians and engineers. I just thought of myself as a graphic designer but through this experience I improved my confidence and really got to explore what I was capable of.
The Matrix Textile laser was the first to cut and mark apparel pattern pieces while lasering denim whiskers (the worn appearances) or textile/graphic designs. A bundle stacking system was attached to the laser, automatically collecting and stacking the cut pieces. To create the CAD files for production, I had to learn how to use SEI branded software programs, Engenius and Icaro. Engenius was used for virtually assembling pattern pieces in a 3D generator and applying designs to them. Icaro was then used to create the production files that were eventually loaded to but cut and burned in the Matrix.
SEE VIDEO BELOW
Video by Tamer Seker
3D Design Software Engenius process
3D Rendering of jean
Stitching of garment in Engenius
Generated production file for Icaro
MATRIX TEXTILE LASER PROJECT SPOTLIGHT:
“EVERLANE LOS ANGELES” WAISTBAND JEAN

Finished production pieces coming off the bundle stacker
Competed raw garment sewn
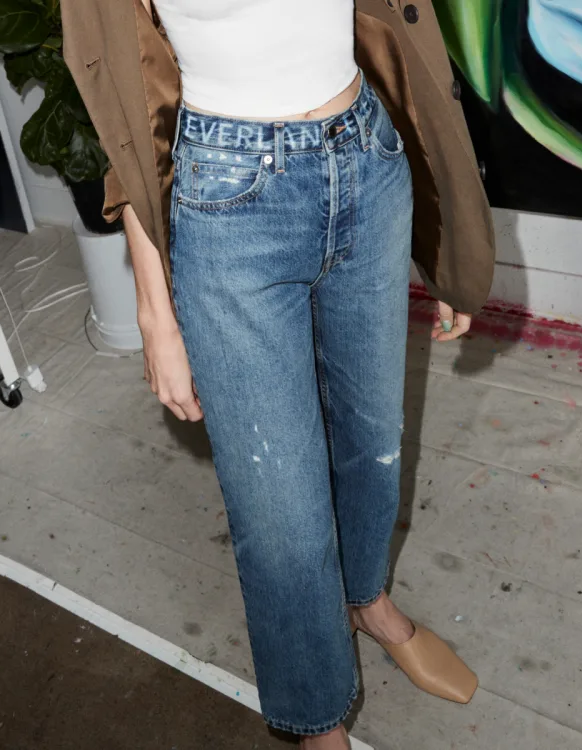
Finished product